Manage plant productivity
ก่อนจะเริ่มการบริหารจัดการผลผลิตของโรงงานให้มีผลผลิตสูงสุด ค่าใช้จ่ายในการผลิตต่ำสุดจำเป็นต้องรู้รูปแบบของโรงงานและแฟคเตอร์ที่สำคัญที่มีผลต่อสมรรถนะของการบริหารผลผลิตและต้นทุนการผลิต การรวบรวมข้อมูลที่จำเป็นให้พร้อมและเพียงพอ รวมถึงการเรียนรู้แนวปฎิบัติที่ดีในการบริหารจัดการ
การวัดผลผลิตของโรงงาน (Plant productivity)
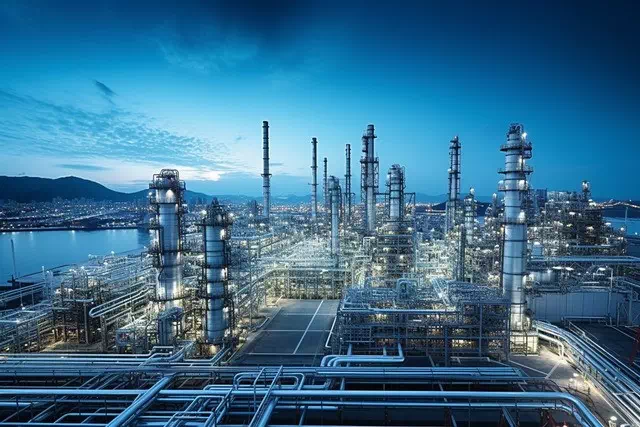
Productivity คือการวัดปริมาณผลผลิตที่โรงงานผลิตได้ต่อค่าใช้จ่ายที่จ่ายไปยิ่งทำให้ค่าใช้จ่ายต่อหน่วยการผลิตต่ำ (Low production cost) จะทำให้การขายสินค้าทำได้ง่ายขึ้น มีกำไรจะสูง จึงเป็นความสามารถในการจัดการของผู้บริหาร ที่จะต้องทำให้การผลิตใด้สูงสุด ต้นทุนต่อหน่วยต่ำสุด ซึ่งจะต้องควบคุมตัวแปรที่สำคัญต่างๆดังที่จะกล่าวต่อไปนี้ให้ได้
Plant หรือโรงงานสร้างมาเพื่อการผลิต การวัดสมรรถนะ (Performance) ของโรงงานคือการวัดผลผลิตเป็นหลัก (Productivity) โดยการวัดผลผลิต (Productivity) ของผลิตภัณฑ์ที่กำหนดของโรงงาน ในระยะเวลาที่กำหนด (Period) เช่นผลิตได้ 500,000 ตันต่อปี โดยมีเวลาเดินเครื่อง 300 วัน (มีเวลาหยุดเครื่องเพื่อการซ่อมบำรุง 65 วัน) มีการใช้วัตถุดิบ (Raw material) และพลังงาน (Energy) ตามกำหนด (Design figure) มีของเสีย (By product หรือ Waste) เกิดขึ้นน้อย มีการเดินเครื่องได้ต่อเนื่อง (Continuous) ไม่ต้องหยุดซ่อมบ่อย (Interrupt) อัตราการใช้งานได้ (Utilization rate) สูง อุปกรณ์ทุกตัวเดินเครื่องที่ประสิทธิภาพสูง และมีความเชื่อถือได้ (Reliability) มีความพร้อมจะใช้งาน (Availability) ซึ่งผู้รับเหมาจะต้องออกแบบ และก่อสร้างตามมาตรฐานทางวิศวกรรม (Engineering code and standard) มีอุปกรณ์สำรองที่เหมาะสมและเพียงพอเพื่อให้โรงงานสามารถสร้างผลผลิต (Product yield) ได้ตามต้องการ และมีความปลอดภัยในการใช้งาน (Safe to operate)
เนื่องจากโรงงานมีอุปกรณ์หลายแบบ หลายตัว ทำงานเกี่ยวพันกันอย่างซับซ้อน แต่ละตัวมีกำหนดการบำรุงรักษา (Maintenance) ไม่เหมือนกัน ไม่พร้อมกัน ปัญหาในการใช้งาน (Trouble) ที่เกิดของแต่ละอุปกรณ์แต่ละตัว ก็เกิดขึ้นได้ตลอดเวลา การวางแผนบำรุงรักษาจึงต้องทำเป็นอย่างจริงจัง การแก้ปัญหที่เกิดขึ้นต้องทำอย่างรวดเร็ว เพื่อไม่ให้กระทบต่อผลผลิต และเป้าหมายของโรงงาน
เนื่องจากผู้รับเหมาต้องออกแบบและก่อสร้างโรงงานให้ใด้ผลผลิตตามที่รับประกัน (Performance guarantee) ใว้กับเจ้าของโรงงาน จึงต้องจัดหาอุปกรณ์ที่มีคุณลักษณะ (Specification) เผื่อใว้มากกว่าคุณสมบัติที่ต้องการ เมื่อมีการทดสอบสมรรถนะการผลิต จะมั่นใจได้ว่าจะผ่านการทดสอบ
การเดินเครื่องใช้งานระยะแรกๆ จะมีปัญหาของกระบวนผลิตเอง และปัญหาของอุปกรณ์ เพราะผู้ใช้ยังไม่รู้จักกระบวนการผลิต ระบบ และอุปกรณ์ดีพอ ทักษะการเดินเครื่อง การใช้อุปกรณ์ และการบำรุงรักษาก็ยังไม่ดีพอ ความผิดพลาดจึงมีมาก นอกจากนี้บางระบบและอุปกรณ์เองก็มีปัญหาในตัว (Bad actor)ต้องหยุดอุปกรณ์เพื่อวิเคราะห์ หาทางแก้ไข จนว่าจะแก้ไขปัญหาได้หมด การเดินเครื่องจึงจะค่อยๆทำได้ต่อเนื่องขึ้น กระบวนการแก้ไขปัญหาความเชื่อถือได้ (Reliability) ทำให้เครื่องจักรมีความพร้อมใช้งาน (Availability) นี้โดยทั่วไปจะใช้เวลา 1-3 ปี
เนื่องจากการออกแบบของผู้รับเหมาจะเผื่อค่าในการออกแบบ (Safety design margin) ของระบบและอุปกรณ์ใว้สูง เพื่อให้การทดสอบการประกัน (Guarantee) ความสามารถในการผลิต (Production capacity) ของโรงงานผ่านได้ จึงมีความเป็นไปได้ที่ผลผลิตของโรงงานที่ทำได้จริง (Maximum capacity) จะมีค่าสุงกว่าค่าที่ออกแบบใว้ (Design capacity)
เมื่อเดินเครื่องไปได้ระยะหนึ่ง เจ้าของโรงงานจะทำการเพิ่มการผลิต (Increase capacity) โดยการปรับปรุง (Revamp หรือ Improvement) โรงงาน โดยใช้คุณสมบัติส่วนเกินของอุปกรณ์ที่ผู้รับเหมาทำใว้ให้ และทำการปรับปรุงอุปกรณ์ (Modify) ที่ยังขาดคุณลักษณะ ไม่ได้ความต้องการของกระบวนการผลิต จะทำให้ผลผลิตใหม่สูงกว่าเก่าโดยที่ลงทุนเพิ่มไม่มาก
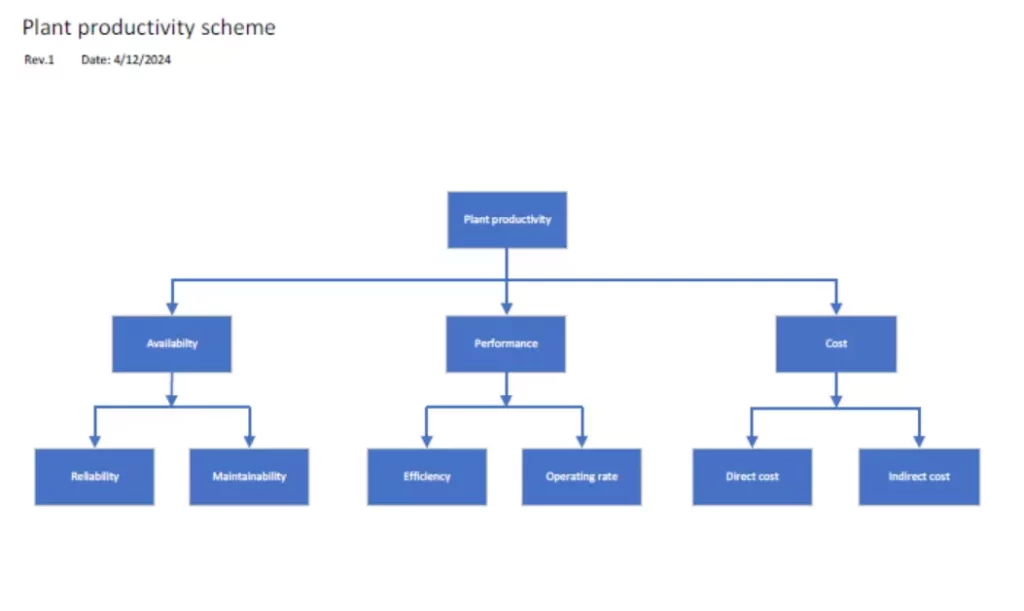
ผลผลิตของโรงงานจะขึ้นกับแฟคเตอร์หลักที่สำคัญ คือความพร้อมในใช้งาน (Availability) สมรรถนะของโรงงานและเครื่องจักร (Performance) และค่าใช้จ่ายในการผลิต (Cost) และแฟคเตอร์สนับสนุนย่อยๆ เช่นความเชื่อถือได้ (Reliability) ความสามารถในการซ่อมบำรุง (Maintainability) ประสิทธิภาพของอุปกรณ์ (Efficiency) ระดับการเดินเครื่องเพื่อใช้งาน (Operating rate) ค่าใช้จ่ายทางตรงและทางอ้อม (Direct and indirect cost)
ปริมาณผลผลิตของโรงานยิ่งมาก จะทำให้ต้นทุกการผลิตยิ่งต่ำ กำไรจะสูงขึ้น เพราะค่าใช้จ่ายคงที่เท่าเดิมไม่ว่าจะผลิตเท่าไร ดังนั้นการวางแผนบำรุงรักษา การจัดหาอะไหล่ให้เพียงพอ เพื่อทำให้อุปกรณ์มีความเชื่อถือได้สูง ใช้งานได้ จึงต้องทำให้มีประสิทธิผล
นอกจากการวัดผลผลิตโดยรวม (Plant productivity) ซึ่งเป็นหัวใจสำคัญแล้ว แล้วยังต้องวัดสมรรถนะของระบบและอุปกรณ์ต่างๆในโรงงาน เพราะเป็นตัวสนับสนุน (Contribute) ให้เกิดผลผลิตรวม (Plant productivity) ของโรงงาน ระบบและอุปกรณ์ทุกตัวจะต้องมีสมรรถนะดีตามที่ได้ออกแบบและคาดหวังใว้
การวัดสมรรถนะ (Performance) ในโรงงานต้องวัดใน 5 ระดับ
1 .วัดสมรรถนะของโรงงาน วัดผลผลิตโดยรวมที่โรงงานจะผลิตออกมาได้ (Productivity, Ton per year-TPA) และค่าใช้จ่ายต่อหน่วยต่ำ (Production cost)
2. วัดสมรรถนะของระบบ
3. วัดสมรรถนะของอุปกรณ์ วัดประสิทธิภาพของเครื่องจักร (Efficiency) ฮีทเรท (Heat rate) เอนเนอจี้เรท (Energy rate) ความเชื่อถือได้ (Reliability) ความพร้อมใช้งาน (Availability) เป็นต้น
4. วัดสมรรถนะของอุปกรณ์ย่อย เช่นความชื่อถือได้ (Reliability) และความมีประสิทธิผลของการใช้อุปกรณ์ (Overall equipment effective)
5. วัดสมรรถนะของอะไหล่ ความคงทน อายุไช้ได้นาน
แต่จะวัดได้แค่ใหนขึ้นกับทัศนคติและความรู้ของผู้บริหาร ความรู้และทักษะของคน เครื่องมือ กำลังคนที่มี ความยุ่งยากและความคุ้มค่าในการวัด
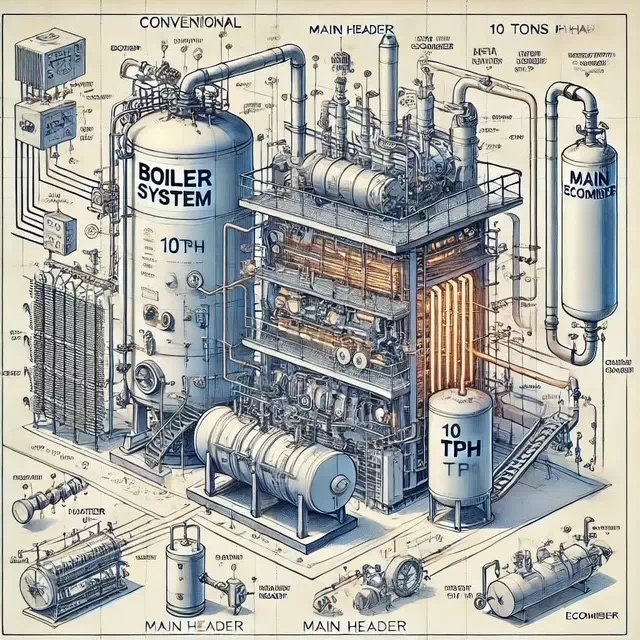
ผังแสดงรูปแบบกระบวนการผลิตของโรงงานผลิตไฟฟ้าจากถ่านหินอย่างง่ายๆโดยให้เห็นความสัมพันธ์ของอุปกรณ์สำคัญ
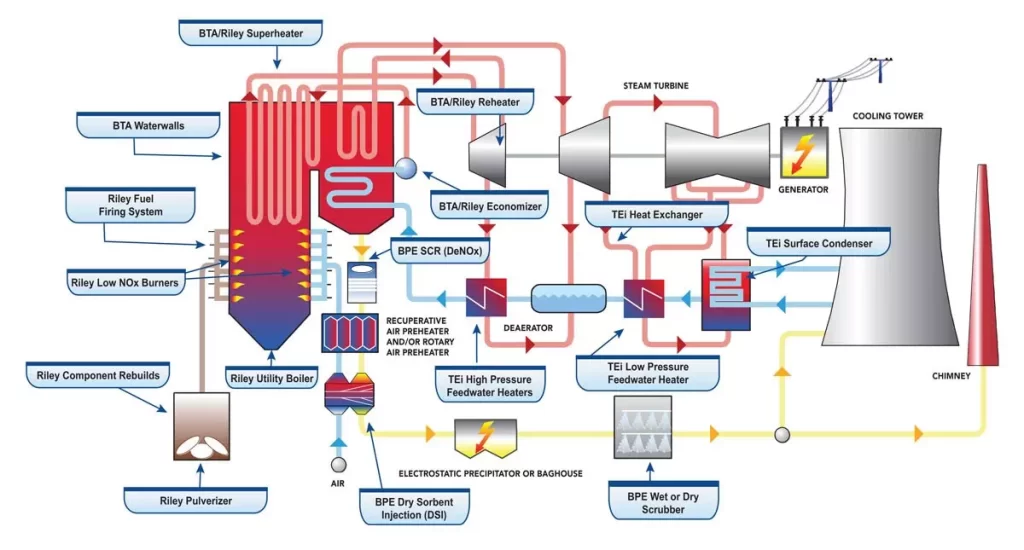
โรงงานส่วนใหญ่จะประกอบด้วยระบบท่อที่ต่อกับอุปกรณ์ต่างๆ เช่นปั๊ม คอมเพรสเซอร์ เทอร์ไบน์ เครื่องกวน เครื่องถ่ายเทความร้อน ถังปฎิกริยา วาล์ว เป็นต้น ที่อยู่ในกระบวนการผลิต (Production process) เพื่อนำวัตถุดิบเข้าสู่กระบวนการผลิต ใช้พลังงานเพื่ออัด/ลดความดัน เพิ่ม/ลดอุณหภูมิ เพื่อแยก/รวม และแตกตัว/ทำปฎิกริยาในกระบวนการผลิต เพื่อให้ได้ผลิตภัณฑ์ (Products) ตามที่ต้องการ
โรงงานจะประกอบด้วยระบบ และอุปกรณ์ข้างต้นมากมาย หลายแบบ หลายขนาด หลายๆคุณสมบัติความซับซ้อนแล้วแต่ชนิดของกระบวนการผลิต บางโรงงานซึ่งมีแก๊สไวไฟ แก๊สพิษ ลักษณะโรงงานจะต้องการความปลอดภัยสูง อุปกรณ์ที่ใช้ก็ยิ่งซับซ้อนมากยิ่งขึ้น
Process flow diagram (PFD)
โรงงานจะเริ่มการออกแบบ (Design) จากการวางแนวคิด (Conceptual design) ด้านกระบวนการผลิต (Production process flow) เป็นกระบวนการง่ายๆ (Simple process flow diagram, PFD) เพื่อทำการศึกษาการบาลานส์ที่ดีที่สุด (Optimum balance) ของวัสดุกับพลังงานที่ใช้ในกระบวนการผลิต (Material or mass and energy balance) เพื่อให้ได้ผลผลิตตามต้องการ และเพื่อดูว่าใช้วัตถุดิบอะไรบ้าง มีของเสียอะไรออกมาบ้าง ก่อนการออกแบบในรายละเอียด PFD จะมีของระบบต่างๆแยกกัน
จะต้องรู้ว่าโรงงานต้องใช้สาธารณูปโภค (Utility) อะไรบ้าง ใช้พลังงาน (Energy) อะไรบ้าง ในการเปลี่ยนวัตถุดิบ ผ่านกระบวนการผลิต (Production process) เพื่อให้ได้ผลิตภัณฑ์ (Products) ตามต้องการ มีผลิตภัณฑ์พ่วง (By products) ตามมาบ้าง มีของเสีย (Waste) อะไรบ้าง
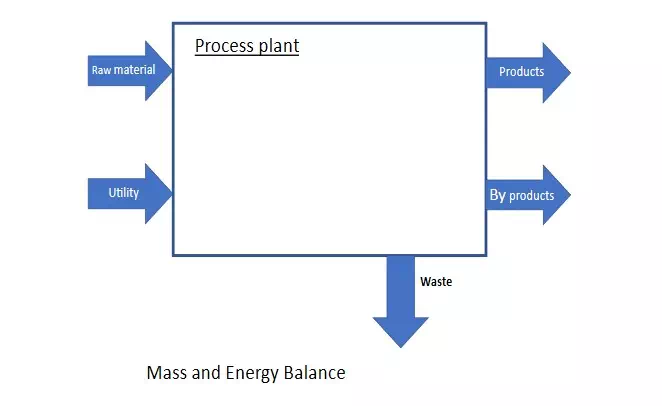
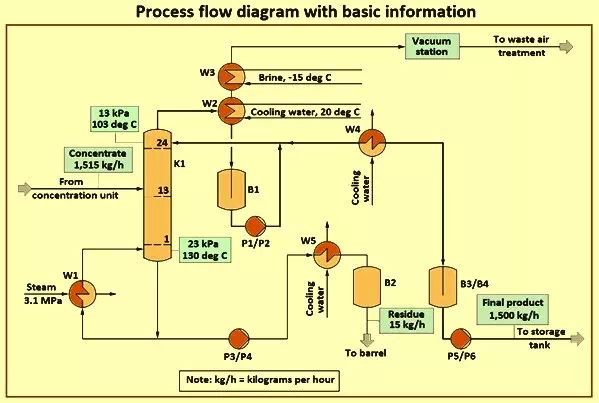
ระบบการผลิตโรงงานจะมีระบบการผลิตหลักๆดังนี้
1. ระบบผลิตหลัก (Main process) คือกระบวนการผลิต (Production process) หลัก อาจจะมีหลายๆระบบ (PFD) ประกอบต่อกัน เพื่อการจัดการกับวัสดุและพลังงานที่ต้องใช้ในกระบวนการผลิต เพื่อแปลงวัตถุดิบเป็นผลิตภัณฑ์ที่ต้องการ
2. ระบบสนับสนุน (Supporting process, Utility process) คือระบบที่ช่วยให้กระบวนการผลิตหลักทำงานได้ เช่น
- ระบบผลิตไอน้ำ
- ระบบน้ำที่ใช้ในโรงงาน
- ระบบน้ำหล่อเย็น
- ระบบน้ำที่ใช้ในกระบวนการผลิต
- ระบบน้ำดิบ
- ระบบกำจัดน้ำเสีย
- ระบบระบายน้ำฝน น้ำทิ้ง
- ระบบลมอัด
- ระบบลมแห้งสำหรับระบบควบคุม
- ระบบไฟฟ้ากำลัง
- ระบบควบคุมกระบวนการผลิต
- ระบบถังเก็บวัตถุดิบและผลิตภัณฑ์
- ระบบขนส่งวัสดุในการผลิต
3. ระบบโครงสร้างพื้นฐาน(Infrastructure) คือระบบอำนวยความสดวกในการทำงาน เช่น
- อาคารซ่อมบำรุง
- อาคารเก็บวัสดุในการผลิต
- อาคารเก็บอะไหล่
Piping and instrument flow diagram (PID)
คือ การนำ PFD มาทำการออกแบบระบบท่อ อุปกรณ์ และระบบควบคุมทั้งหมดที่ใช้ในโรงงาน PID จะมีจำนวนมาก ต้องครอบคลุมทุกๆ PFD เป็นโครงสร้างหลักของโรงงาน การเลือกอุปกรณ์ต่างมาใช้งานต้องมีความเหมาะสม เพื่อให้โรงงานทำงานได้โปรดัคส์ คุณภาพ ประสิทธิภาพ และเซฟตี้ตามต้องการ
จาก PID ผู้ออกแบบจะใช้เป็นข้อมูลในการประเมินราคาค่าก่อสร้างโรงงาน ซึ่งราคาจะขึ้นกับคุณสมบัติ (Specification) ของอุปกรณ์และวัสดุที่ใช้ และความปลอดภัยของระบบผลิต เช่น
- ชนิดของโรงงานและกำลังผลิต (Capacity)
- ความยืดหยุ่นของกระบวบการผลิต (Flexibility)
- ความชื่อถือได้ของกระบวบการผลิต (Reliability)
- ประสิทธิภาพของกระบวบการผลิต (Efficiency)
- ความปลอดภัยของกระบวบการผลิต (Safety)
- ความเป็นมิตรต่อสิ่งแวดล้อม (Environment)
- คุณลักษณะของระบบและอุปกรณ์ (Specification of equipment)
- ความต้องการอื่นของเจ้าของ (Specific requirements)
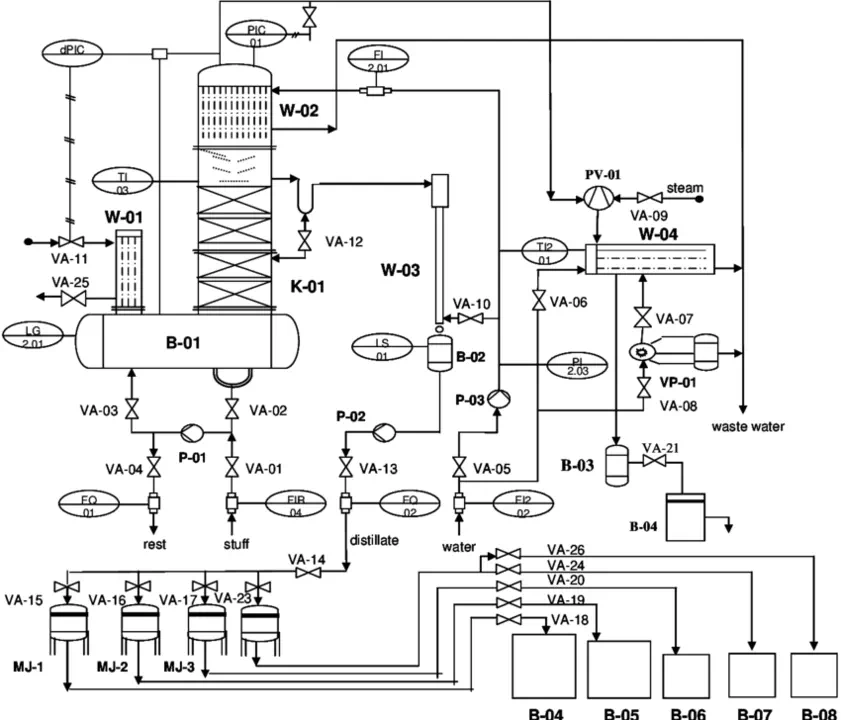
PID จะบอกอุปกรณ์ทั้งหมดที่ใช้ในกระบวนการผลิตของโรงงานและคุณสมบัติย่อๆ มีระบบการตั้งชื่อเรียก (Equipment name) ชื่อระหัสประจำตัวอุปกรณ์ (Tag number) กรุ๊ปเป็นประเภท (Type) เป็นหมวดหมู่ (Grouping) เป็นลำดับ (Sequence number) ในแต่ละระบบ (System) แต่ละ PID ซึ่งจะสอดคล้องกันในแต่ละโรงงาน
โดยจะแบ่งเป็นลำดับดังนี้
- Plant ชื่ออะไร
- System มีชื่อระบบย่อยในกระบวนการผลิต (System) มีระบบอะไรบ้าง
- Equipment แต่ละระบบประกอบด้วยอุปกรณ์และเครื่องมือควบคุม (Instrument) อะไรบ้าง
การสร้างโรงงาน(Plant construction)
เจ้าของโรงงานโดยที่ปรึกษาทางวิศวกรรมต้องทำการออกแบบเบื้องต้น ทำ PFD และจัดทำคุณลักษณะของโรงงานและอุปกรณ์ให้เสร็จก่อน แล้วให้ผู้รับเหมาเสนอราคาการออกแบบในรายละเอียดและค่าก่อสร้างให้พิจารณา ซึ่งประกอบด้วย
Equipment ชื่อและจำนวนอุปกรณ์และเครื่องมือควบคุมแต่ละชนิดในระบบ
Specification รายละเอียดคุณสมบัติของโรงงาน ระบบ และอุปกรณ์ทุกตัวเพื่อจะจัดหาใด้อย่างถูกต้อง
AVL – Approved vendor list คือลิสท์รายชื่อผู้ผลิตหรือผู้ขายอุปกรณ์ต่างๆที่ใช้ในระบบคัดเลือกจากผู้ผลิตที่ใด้ผ่านการตรวจสอบคุณสมบัติแล้ว และได้รับอนุมัติ (Approved) จากเจ้าของโครงการให้เลือกใช้ได้ในโรงงาน โดยมากจะเลือกจากผู้ผลิตที่มีชื่อเสียง มีประสบการณ์ มีความเชื่อได้มีผู้ใช้งานอยู่แพร่หลายผู้รับเหมาสามารถเสนอนอกจาก แต่เจ้าของโครงการต้องอนุมัติให้ดำเนินการได้
เมื่อก่อสร้างเสร็จแล้วผู้รับเหมาจะทำข้อมูลเหล่านี้ให้เจ้าของงาน
เมื่อก่อสร้างเสร็จ ผู้รับเหมาจะต้องมอบข้อมูลเหล่านึ้ให้เจ้าของโรงงาน เพื่อเป็นประวัติและใช้ดูแลโรงงาน
PFD and PID Equipment list คือลิสท์รายชื่ออุปกรณ์ทั้งหมด แบ่งเป็นชนิด
Equipment installation base รายการอุปกรณ์ ชื่อผู้ผลิตหรือผู้ขายอุปกรณ์ติดตั้งจริงในโรงงาน ผู้รับเหมาจะจัดเตรียมให้ แยกประเภทใว้ แยกเป็นหมวดหมู่ เพื่อประโยชน์ในการควบคุม การติด การจัดซื้อ จัดส่ง และการติดตามประสานงาน (เช่น เครื่องหมุน อุปกรณ์โปรเซส วาล์ว เอกแพนชั่นจอยท์ เป็นต้น) ซึ่งเอกสารเหล่านี้ผู้รับเหมาจะต้องให้ทางโรงงานใว้ใช้งานเมื่อเสร็จโปรเจคท์
Tag number คือชื่อและหมายเลขประจำตัวอุปกรณ์ จัดเรียงอย่างเป็นระบบ ให้รู้ว่าเป็นอุปกรณ์ในระบบอะไร หมายเลขอะไร เป็นอุปกรณ์ตัวหลักหรือตัวสำรอง
Name plate คือป้ายคุณสมบัติย่อๆของอุปกรณ์ที่ติดมากับตัวอุปกรณ์ ระบุหมายเลขลำดับที่ในที่ผลิต (Serial number) ของผู้ผลิต
Data sheet คือคุณสมบัติ (Specification) เพื่อการจัดซื้ออุปกรณ์นั้นๆโดยละเอียด ระบุรูปแบบ และคุณสมบัติอย่างละเอียดของอุปกรณ์หลักและอุปกรณ์ย่อยๆ
Safety data sheet คือคุณสมบัติและคำแนะนำด้านคุณสมบัติและความปลอดภัยของสารที่ใช้เพื่อการผลิต
Drawing แบบพิมพ์เขียวของโรงงาน ระบบ และอุปกรณ์
Inspection record คือข้อมูลการตรวจสอบโรงงาน ระบบ และอุปกรณ์ ตามแผนการประกันคุณภาพ (Quality assurance)
Test record คือข้อมูลผลการทดสอบโรงงาน ระบบ และอุปกรณ์ ตามคุณสมบัติที่ได้กำหนดใว้
Drawing คือแบบการก่อสร้าง แบบอุปกรณ์ต่างๆ
Operating and maintenance manual คือคู่มือการเดินเครื่องใช้งานและการบำรุงรักษาของโรงงาน ระบบ และอุปกรณ์ต่างๆ
Record book คือไฟล์การรวบรวมข้อมูลในการสร้างโรงงาน การตรวจสอบ การทดสอบ แบบพิมพ์เขียว คู่มือการเดินเครื่องใช้งาน และการบำรุงรักษา แยกเป็นหมวดหมู่ ใว้ใช้อ้างอิงในการใช้งานของโรงงาน
Spare part list คือรายลิสท์ของอะไหล่ที่ผู้รับเหมาและผู้ผลิตเครื่องจักรแนะนำ(Recommended) ให้มีเก็บสำรอง (Spare stock) ใว้ใช้งาน รวมทั้งการทำรายการอะไหล่ของอุปกรณ์ที่ใช้แทนกันได้ (Spare part interchangeability record, SPIR) ลิสท์
Catalog คือแคทตาลอกของอุปกรณ์ต่างๆในโรงงาน
Purchasing specification คือข้อมมูลระบุคุณสมบัติ รายละเอียดที่จำเป็นของอุปกรณ์ที่จะสั่งซื้อ
Plant equipment by arrangement
เนื่องจากเป็นระบบการผลิตเป็นการผลิตต่อเนื่อง อุปกรณ์บางตัวจึงต้องมีตัวสำรอง ใว้เผื่อตัวหนึ่งต้องหยุดซ่อม หรือบำรุงรักษา จะมีตัวที่เดินเครี่องในระบบได้ตลอดเวลา คือเป็น
1. ตัวที่เดินเครื่องใช้งาน (Active unit, ใช้สัญลักษณ์ A, B, C,…)
2. ตัวที่ติดตั้งสำรองใว้ (Stand by unit, ใช้สัญลักษณ์ R)
การติดตั้งบางครั้งก็ใช้หลัก 100 A : 100R
50A + 50B : 50R
35A + 35B + 35C : 35R
เป็นต้น
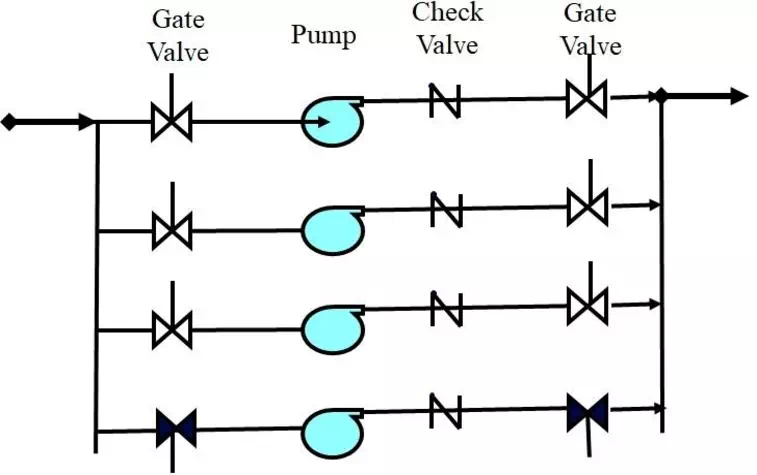
ทั้งนี้ขึ้นกับผู้ออกแบบ ลักษณะของกระบวนการผลิต ความคิดและประสบการณ์ด้านความเชื่อถือได้ระบบของผู้ออกแบบ และประสบการณ์และความต้องการของผู้ใช้งาน
ความสำคัญของระบบและอุปกรณ์
ระบบและอุปกรณ์ต่างในโรงงานมีความสำคัญ (Criticality) ต่อระบบการผลิตไม่เท่ากัน โดยเฉพาะในกระบวนการผลิตที่ต้องทำต่อเนื่อง (Continuous process) อุปกรณ์เหล่านี้จะขัดข้อง (Trouble) ทำงานไม่เต็มที่ (Partial load) หรือหยุดเดิน (Shutdown) ไม่ได้ เพราะจะทำให้เกิดความเสียหายต่อการผลิต ต่อการจัดส่งสินค้าให้ลูกค้า ถ้าส่งให้ไม่ได้ จะสูญเสียลูกค้าไปในที่สุด
1. อุปกรณ์ที่สำคัญมาก (Critical equipment)
ได้แก่อุปกรณ์ที่สำคัญ และจำเป็นต้องมีในกระบวนผลิตหลัก ส่วนใหญ่จะราคาแพงมาก มีตัวเดียว ไม่เพราะไม่คุ้มค่าที่จะมีอุปกรณ์สำรอง หากขัดข้อง หรือฟังค์ชั่นไม่ใด้เต็มที่ จำเป็นต้องหยุดเครื่อง หรือเกิดความไม่ปลอดภัยต่อบุคคลหรือทรัพย์สินที่จะเดินเครื่องต่อไป
2. อุปกรณ์สำคัญต่อกระบวนการผลิต (Essential equipment) มีตัวสำรองใว้กับที่ สามารถเดินเครื่องแทนได้ทันที (Hot stand by) โดยไม่ต้องลดกำลังผลิต แต่ต้องลดกำลังผลิต หรือลดประสิทธิภาพลง
3. อุปกรณ์จำเป็นต่อกระบวนการผลิต (Important equipment) มีตัวสำรองใว้กับที่ หรือสำรองในคลังพัสดุ (Warehouse spare) ถ้าขัดข้อง หรือไม่ฟันค์ชั่น ไม่ต้องหยุดเครื่องหรือลดกำลังผลิตลง แต่ต้องรีบแก้ไข เพราะความเชื่อถือได้ (Reliability) ของระบบหรือโรงงานจะลดลง
4. อุปกรณ์ทั่วๆไป (General equipment) มีใว้เพื่อสนับสนุนการผลิต ให้สดวกขึ้น
ความเร่งด่วนในการซ่อม(Operation priority)
1. งานฉุกเฉิน (Emergency work) คืองานที่หากไม่รีบทำ ไม่รีบแก้ไข จะเกิดความเสียหายต่อการผลิต ระบบผลิตอย่างรุนแรง อาจจะมีผลให้ต้องหยุดซ่อมนาน ต้องหยุดขบวนการผลิต ต้องลดปริมาณการผลิต การผลิตมีประสิทธิภาพต่ำ ค่าใช้จ่ายในการผลิตสูง ไม่ปลอดภัยต่อการเดินเครื่องต่อไป ส่วนใหญ่จะเกิดกับ Critical equipment และอุปกรณ์ควบคุมความปลอดภัย
2. งานสำคัญ (Important work) คืองานของ Important equipment มีตัวสำรอง งานรอทำได้บ้าง แต่ไม่นาน ถ้าไม่รีบทำให้เสร็จ ความเชื่อถือได้ (Reliability) ของโรงงานจะน้อยลง หรือกิดความเสียหายตามมา
3. งานที่ไม่เร่งด่วน (Normal work) งานของอุปกรณ์ทั่วๆไปที่ไม่สำคัญต่อการผลิตมาก รอทำได้แต่ต้องทำให้เสร็ดในเวลาที่ระบุ
ทางหน่วยงานบำรุงรักษาต้องเตรียมอะไหล่ และกำลังคนให้พร้อมตลอดเวลาเพื่อแก้ปัญหาเหล่านี้ นอกจากนี้ต้องยังต้องทำงานตามแผนการบำรุงรักษาป้องกัน
กลยุทธ์ในการบำรุงรักษา (Maintenance strategy)
การเลือกวิธีทำงาน (Strategy) ของอุปกรณ์แต่ละชนิดเป็นเรื่องสำคัญ เพราะมีผลต่อความเชื่อถือได้และค่าใช้จ่ายในการเดินเครื่อง ซึ่งขึ้นกับกับคำแนะนำของผู้ผลิตอุปกรณ์ ประสบการณ์ และความเชื่อของผู้บริหาร อุปกรณ์มีความสำคัญต่อระบบผลิตแตกต่างกัน กลยุทธ์การบำรุงรักษาจึงไม่เหมือนกัน แต่ทุกๆอุปกรณ์จะต้องได้รับการดูแล
กลยุทธ์การบำรุงรักษามีดังนี้
1. Preventive maintenance การบำรุงรักษาแบบวางแผนล่วงหน้า ก่อนที่อุปกรณ์ อุปกรณ์ย่อย หรืออะไหล่จะสึกหรอ หรือเสื่อมจนใช้การไม่ได้หรือไม่ฟันค์ชั่น วิธีนี้แผนการของแต่ละอุปกรณ์จะมีกำหนดการตายตัว
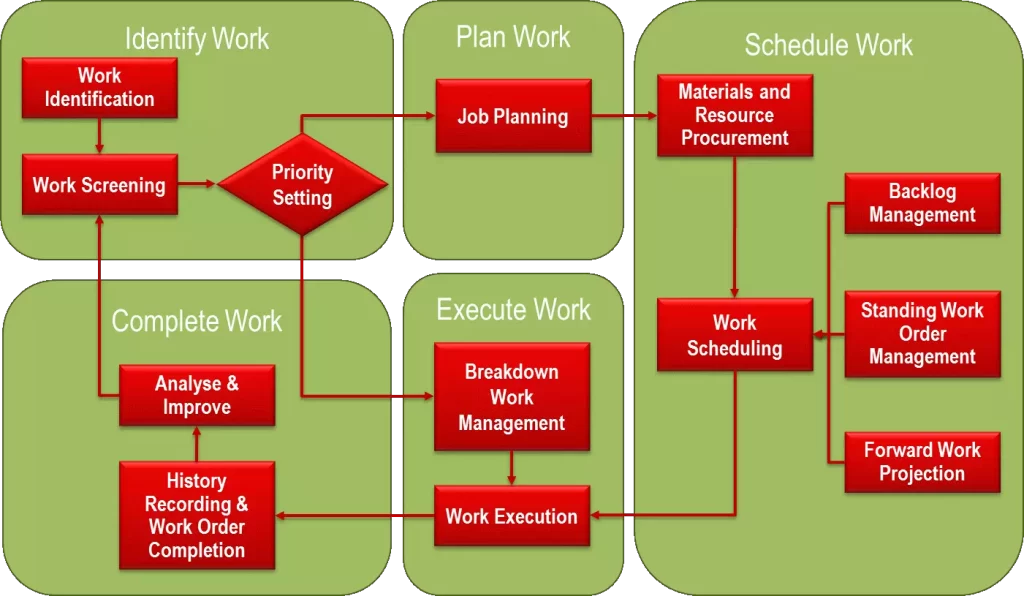
2. Predictive maintenance การบำรุงรักษาแบบทำนายล่วงหน้าว่าอุปกรณ์ อุปกรณ์ย่อย หรืออะไหล่จะสึกหรอ หรือเสื่อมจนใช้การไม่ได้หรือไม่ฟันค์ชั่น เป็นวิธีการที่ต้องใช้เครื่องมือพิเศษและความชำนาญช่วยวิเคราะห์จากข้อมูลหรืออาการทีตรวจพบระหว่างเดินเครื่อง วิธีนี้จะช่วยยืดแผนการบำรุงรักษาออกไป ลดค่าใช้จ่ายค่าซ่อมและอะไหล่
3. Corrective maintenance (Run to fail) การไม่ทำอะไรเลย เดินเครื่องจนอุปกรณ์ อุปกรณ์ย่อย หรืออะไหล่จะสึกหรอ หรือเสื่อมจนใช้การไม่ได้ ต้องหยุดเครื่องลงมาซ่อม คือเสียแล้วจึงซ่อม ใช้กับอุปกรณ์ที่ไม่สำคัญมาก การเสียหายมีไม่มาก
4. Combination strategy maintenance เป็นการผสมกลยุทธ์ทั้งสาม
กำหนดการหยุดเครื่องเพื่อซ่อมใหญ่ (Major turnaround หรือ Major shutdown หรือ Major outage)
คือการหยุดเครื่องเพื่อซ่อมใหญ่เนื่องจากสาเหตุ
1. สาเหตุจากความขัดข้อง ความเสียหายของอุปกรณ์ (Unplanned shutdown, Forced shutdown, Unplanned outage, Unplan maintenance) ที่เกิดขึ้น ต้องหยุดกระบวนการผลิต หยุดระบบ หรือหยุดอุปกรณ์เพื่อดำเนินการแก้ไข Unplanned shutdown มีผลลบต่อผลผลิตและค่าจ่ายของโรงงาน และจะกระทบต่อการส่งงสินค้าให้ลูกค้า ลูกค้าจะหันไปซื้อจากที่อื่นแล้วไม่กลับมา
2. เพราะแผนการกำหนดซ่อม หรือแผนการบำรุงรักษา (Planned shutdown, Plan outage, Planned maintenance) ที่กำหนดใว้ล่วงหน้าแล้ว ทำให้ควบคุมแผนการส่งสินค้าให้ลูกค้าได้
การกำหนดช่วงเวลาการหยุดเครื่องเพื่อซ่อมใหญ่(Shutdown interval) มีแฟคเตอร์ต่างคือ
1 อายุการใช้งานของอุปกรณ์ ถึงกำหนดต้องเปลี่ยนชิ้นส่วนของเครื่องจักร การเสียหาย (Trouble) เกิดขึ้นบ่อย หรือการเกิดตะกอนเกาะหนา (Fouling) ที่เครื่องถ่ายเทความร้อน (Heat exchanger) จนทำฟังค์ชั่นไม่ได้
จะมีอุปกรณ์ตัวไดตัวหนึ่งที่เดินเครื่องต่อไปไม่ได้ จะเป็นตัวกำหนดคาบเวลา (Interval) ของการหยุดเครื่องเพื่อซ่อมใหญ่ (Major shutdown) คาบเวลาการซ่อมใหญ่จะมีเป็นระยะๆ เช่นทุกปึ ทุก 2 ปี ทุก 3 ปึ เป็นต้น
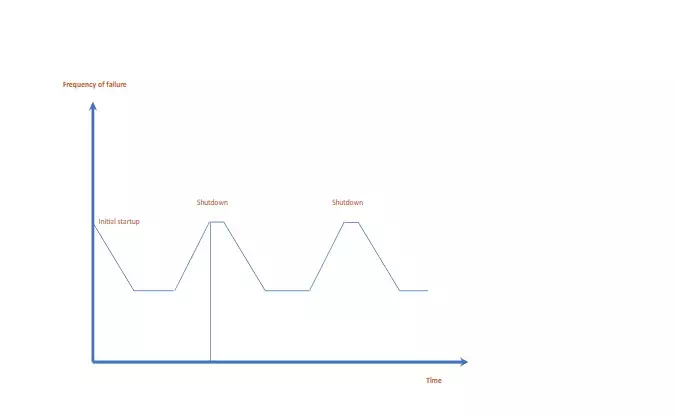
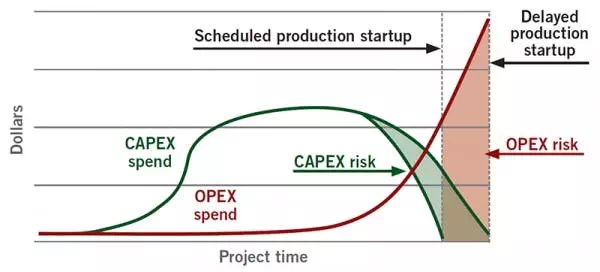
2. การเกาะของตะกรัน โคลน ตะกอน หนาจนมีผลต่อความดัน อุณหภูมิ ความสามารถในการถ่ายเทความร้อนของอุปกรณ์และระบบไม่ดีพอ หรือทำงานไม่ได้ หรือไม่คุ้มทุนที่จะใช้งานต่อ
3. การต้องการตรวจสอบการสึกกร่อน (Erosion) กัดกร่อน (Corrosion) การขัดสี (Abrasion) การบิดเบี้ยว (Distortion) การเสิยรูป (Misshaped) การมีแรงเค้น (Stress) กระทำที่ผิดปรกติของระบบและอุปกรณ์
4. ต้องตรวจสอบต่างระยะเวลา ตามคำแนะนำจากผู้ผลิต (Vendor recommendation)
เนื่องจากอุปกรณ์ในโรงงานมีหลายตัว จะมีตัวที่เป็นสาเหตุใหญ่ในการกำหนดคาบการหยุดเครื่อง
ค่าใช้จ่ายที่เกิดขึ้นจากการหยุดเครื่อง
Down time เวลาที่โรงงานไม่สามารถดำเนินการผลิตได้ เนื่องจากระบบหรืออุปกรณ์ไม่ฟันค์ชั่น (Malfunction) หรือมีปัญหา (Trouble)
Operating loss การสูญเสียของโรงงานเนื่องจากการหยุดเครื่อง การเดินเครื่องที่ลดกำลังผลิต (Derate or reduce capacity) การเดินเครื่องที่ประสิทธิภาพต่ำ (Low efficiency) ทางโรงงานต้องรีบแก้ไขเพื่อให้มีการผลิตตามสมรรถนะ (Design capacity) และมีประสิทธิภาพสูง มีกำไรมากขึ้น
Quantify loss of shut down คือความสูญสียเนื่องจากการหยุดโรงงาน
Total shut down loss = Shutdown cost + Startup cost + Maintenance cost + Opportunity loss
Shutdown opportunity loss คือค่าเสียโอกาสที่จะสร้างรายได้ หรือทำกำไร เนื่องจากการหยุดโรงงาน เป็นความสูญเสียของบริษัท จึงจำเป็นทำให้น้อยที่สุด คือการคุมทั้งจำนวนครั้ง และวันการหยุดเครื่อง
Derate or reduce capacity คือลดกำลังผลิตเนื่องจากปัญหาของอุปกรณ์ ทำให้การผลิตไม่ได้เต็มที่ ค่าใช้ต่อหน่วยของผลิตภัณฑ์จะสูง กำไรจะต่ำลง
Low efficiency คือการเดินเครื่องที่ประสิทธิภาพต่ำกว่าที่ออกแบบใว้ เพราะปัญหาของระบบหรืออุปกรณ์ ทำให้ต้นทุนการผลิตต่อหน่วยสูงขึ้น กำไรจะน้อยลง
การบริหารงานซ่อมใหญ่ (Shutdown management)
เนื่องจากการซ่อมใหญ่มีปริมาณงานมาก ซับซ้อน มีรายละเอียดมาก ใช้เวลาทำงานสั้น อุปกรณ์ทุกชิ้นต้องได้รับการดูแล จึงต้องเตรียมการวางแผนเป็นอย่างดี ทั้งด้านวิธีการ กำลังคน ผู้รับเหมา และอะไหล่ จึงต้องตั้งผู้รับผิดชอบเฉพาะ มีโครงสร้างบริหารแยกออกมา เพื่อทำงานที่สำคัญให้สำเร็จตามเป้าหมาย เพราะต้องทำให้แน่ใจว่าโรงงานจะเดินเครื่องถึงการหยุดเครื่องครั้งต่อไปอย่างไม่มีปัญหา
Plant improvement/ Revamp/ Modification คือการปรับปรุงโรงงาน
โรงงานสร้างโดยผู้รับเหมา ที่ต้องการกำไรจากการสร้างให้มากที่สุด จึงออกแบบให้มีการเผื่อค่าพารามีเตอร์ (Design parameter) ต่างๆให้น้อยที่สุด ทำเพียงเพื่อให้ผ่านการรับประกันสมรรถนะ (Meet guarantee requirements) ที่ให้ใว้กับเจ้าของโครงการ เมื่อใช้งานจริง พบว่าอุปกรณ์มีมาร์จินเหลือ สามารถปรับปรุงกระบวนการผลิตให้มีกำลังผลิต ประสิทธิภาพ และความชื่อถือได้สูงขึ้นได้ ทำให้ได้ประโยชน์ คือ ค่าใช้จ่ายต่ำลง กำไรสูงขึ้น
อุปกรณ์บางตัวมีปัญหา (Trouble, Bad actor) ต้องทำการปรับปรุงให้ดีขึ้นเพื่อความมั่นคงของระบบผลิต
บางครั้งมีเทคโนโลยี่ใหม่ที่สามารถปรับปรุงโรงงาน ระบบผลิต และอุปกรณ์ให้มีกำลังผลิต ประสิทธิภาพ และความชื่อถือได้สูงขึ้นได้ มีความคุ้มที่จะลงทุนเปลี่ยนแปลง
โรงงานจำเป็นต้องเปลี่ยนแปลงตลอดเวลาเนื่องจากความต้องการโปรดัคส์เปลี่ยน วัตถุดิบเปลี่ยน เทคโนโลยี่เปลี่ยน ราคาผลิตภัณฑ์เปลี่ยน อุปกรณ์เก่ามีปัญหา เป็นต้น
การปรับปรุงโรงงาน บ้างครั้งงานใหญ่ บางครั้งงานเล็ก เป็นงานต้องประสานงานของหลายๆหน่ายงาน จึงต้องตั้งผู้รับผิดชอบ และโครงสร้างบริหารขึ้นเฉพาะ บางครั้งต้องมีผู้รับเหมาเข้ามาทำ
การปรับปรุงส่วนใหญ่จะเน้นที่การปรับปรุงเพื่อเพิ่ม Capacity, Efficiency, Reliability, Maintainability, Cost, Safety and environment.
Spare part stock คือการเก็บสำรองอะไหล่ใว้ให้พร้อม สามารถหยิบมาใช้ทันท่วงที เพื่อให้ผลผลิตของโรงงานเป็นไปตามเป้าหมาย